

We are Petro Hydro Pipes Corporation
A company engaged in the engineering and manufacturer of spiral welded steel pipe equipment. It is one of the leading companies in the field of spiral pipe mill technologies.
It has proven itself over and over again with projects located globally for installations of pipe mills and related equipment. It has provided manufacturing solutions in various pipe applications such as water pipes, structural and high-quality oil and gas applications.
With its many years in operation – it has decided to go into the pipe manufacturing business – thus the creation of Petro Hydro Pipes Corporation (PHP).
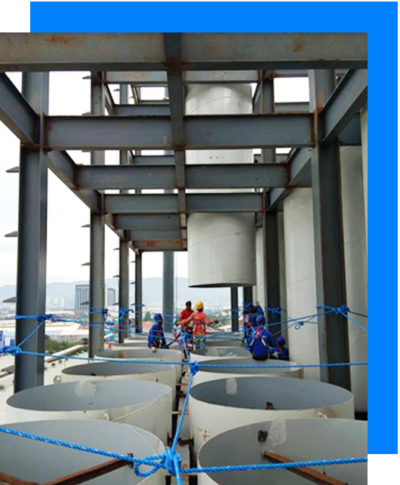
Services Offer
We offer a wide range of services including Include Structural, Pile Casing, Water, and other Construction needs.
Pipe Making
The spiral forming process uses hot rolled steel coil as raw material. The steel uncoiled, leveled passed through a forming station that spirals the steel to the required outside diameter. The spiral seam is then welded both internally and externally by the “submerged arc weld” (SAW) process as part of the forming operation.
The pipe shell thus formed is cut to the required length as it travels out of the forming and welding machine. Spiral welded steel pipes are characterized by its continuous welded helical seam from end to end, which also gives it additional stiffness. Learn more
Raw materials
The raw materials are strip steel coils, welding wire, and flux. Strict physical and chemical tests are required before investment.
Strip head and tail
The strip head and tail are connected by single wire or double wire submerged arc welding, and automatic submerged arc welding is used for repair welding after coiling into steel pipe.
Leveling and edge trimming
Before forming, the strip undergoes leveling, edge trimming, edge planing, surface cleaning and conveying, and pre-bending treatment.
Electric contact pressure gauge
The electric contact pressure gauge is used to control the pressure of the cylinders on both sides of the conveyor to ensure the smooth transportation of the strip.
External or Internal Control
Adopt external control or internal control roll forming.
Welding seam gap control device
The welding seam gap control device is adopted to ensure that the welding seam gap meets the welding requirements, and the pipe diameter, the amount of misalignment and the welding seam gap are all strictly controlled.
Internal welding and external welding
Both internal welding and external welding adopt American Lincoln electric welding machine for single-wire or double-wire submerged arc welding to obtain stable welding specifications.
Shearing the pipes
Shearing the pipes, continuously formed and welded, is sheared automatically to a specified length without stopping the other operations.
Hydrostatic pressure test
Each steel pipe undergoes a hydrostatic pressure test, and the pressure adopts radial seal. The test pressure and time are strictly controlled by the steel pipe hydraulic device. The test parameters are automatically printed and recorded.
Machined accurately
The pipe end is machined to accurately control the verticality of the end face, bevel angle and obtuse edge.
Pipe inspection
Each pipe shall be inspected visually and checked for dimensions. All the welding seams shall be inspected.
Introduction Process
Our Valued Clients
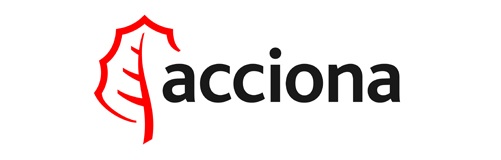
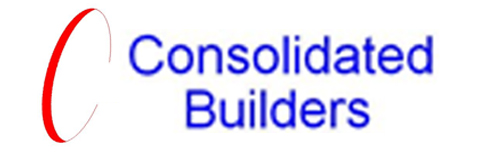
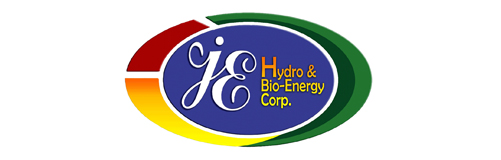
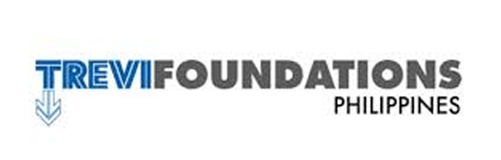
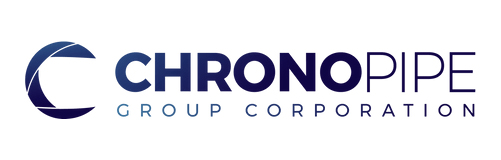